ISO 9001:2015 Quality Management Systems Requirements
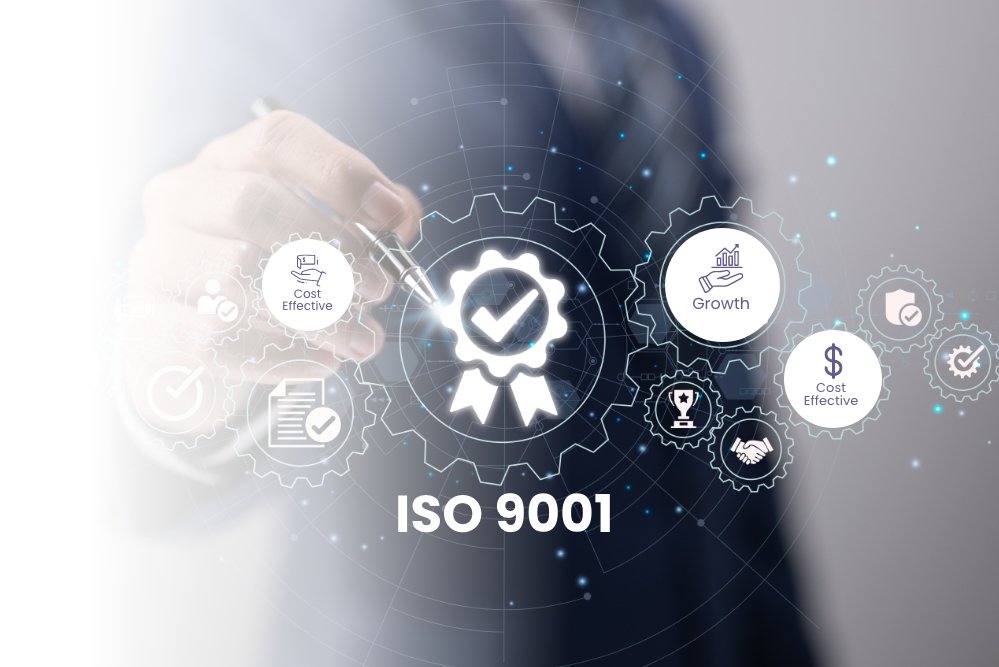
Introduction
In today’s competitive business landscape, maintaining high-quality standards is essential. ISO 9001:2015 is the internationally recognized standard for Quality Management Systems (QMS) that helps organizations meet customer and regulatory requirements. This certification ensures operational excellence, efficiency, and consistent product/service quality.
Understanding ISO 9001:2015
ISO 9001:2015 is part of the ISO 9000 family of standards, focusing on quality management principles to enhance business operations. Since its inception, it has evolved to keep up with modern business practices, ensuring continuous improvement and customer satisfaction.
Why ISO 9001:2015 Certification Matters?
Benefits for Businesses
- Enhances customer trust and satisfaction
- Improves operational efficiency
- Increases market opportunities
- Reduces errors and waste
- Strengthens compliance with regulatory standards
Industry-Specific Advantages
- Manufacturing: Improves product consistency
- Healthcare: Enhances patient safety
- Technology: Ensures software quality standards
- Education: Boosts institutional credibility
Key Principles of ISO 9001:2015
ISO 9001:2015 is built on seven quality management principles:
- Customer Focus – Understanding customer needs and exceeding expectations
- Leadership – Establishing a clear vision for quality excellence
- Engagement of People – Involving all employees in quality improvement
- Process Approach – Managing activities as interconnected processes
- Improvement – Commitment to continuous enhancement
- Evidence-Based Decision Making – Using data for strategic decisions
- Relationship Management – Strengthening supplier and stakeholder partnerships
ISO 9001:2015 Requirements
To achieve certification, businesses must meet the following requirements:
1. Context of the Organization
- Identify internal and external factors affecting quality
- Define customer expectations and regulatory obligations
2. Leadership Commitment
- Assign responsibilities for quality management
- Develop and communicate a quality policy
3. Planning and Risk-Based Thinking
- Identify risks and opportunities
- Establish measurable quality objectives
4. Support and Resource Management
- Allocate resources efficiently
- Train employees for skill enhancement
5. Operational Requirements
- Implement controlled processes for production/service delivery
- Ensure error prevention and corrective actions
6. Performance Evaluation
- Monitor and measure key performance indicators (KPIs)
- Conduct internal audits and management reviews
7. Continuous Improvement
- Address non-conformities
- Implement corrective actions for ongoing enhancement
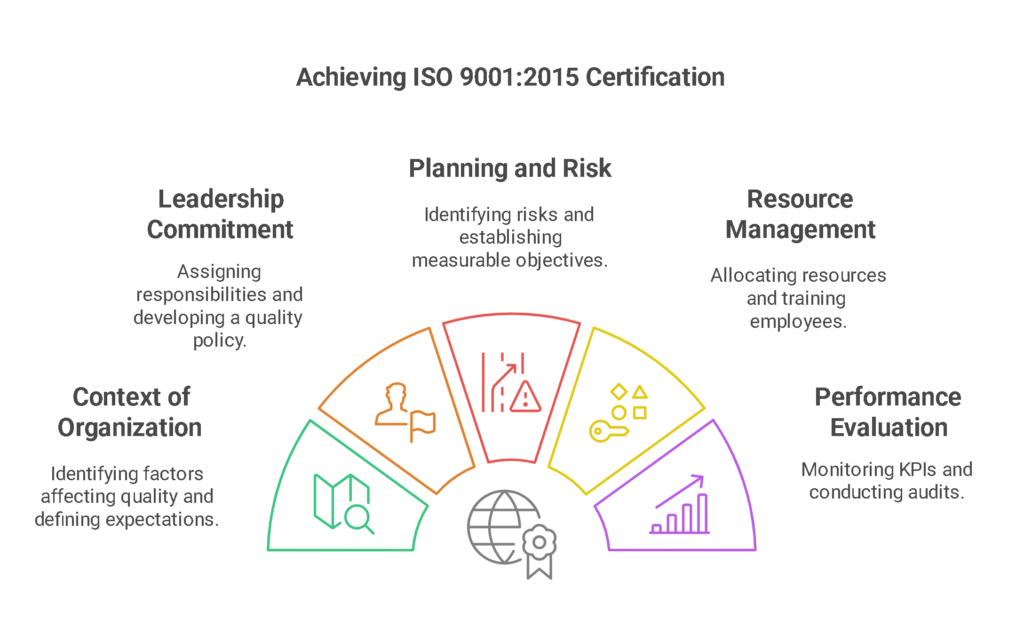
Steps to Achieve ISO 9001:2015 Certification
- Initial Assessment – Understand current quality processes
- Gap Analysis – Identify areas needing improvement
- Implementation Process – Develop and document QMS policies
- Internal Audits – Conduct periodic reviews to ensure compliance
- Certification Audit – Undergo an external audit for certification
Common Challenges and How to Overcome Them
- Lack of Leadership Involvement → Ensure top management commitment
- Employee Resistance → Provide training and clear communication
- Complex Documentation → Use a structured documentation approach
How QA Compliance Assessment Can Help?
At QA Compliance Assessment, we specialize in helping businesses achieve ISO 9001:2015 certification with expert consulting, training, and auditing services. Our experienced professionals ensure a smooth transition to a certified Quality Management System, enabling your business to stay competitive and compliant.
Conclusion
ISO 9001:2015 is a powerful tool for businesses seeking to enhance quality, efficiency, and customer satisfaction. By implementing its principles and requirements, organizations can achieve sustainable growth and operational excellence. Whether you’re just starting or looking to upgrade your QMS, QA Compliance Assessment is here to support your journey.
FAQ
The timeline varies depending on the organization’s size and readiness, but it typically takes 3-6 months.
No, it is voluntary but highly beneficial for credibility and operational efficiency.
Costs depend on business size, complexity, and the certification body chosen.
Yes, businesses of all sizes can implement QMS and achieve certification.
Certification is valid for three years, with annual surveillance audits required.